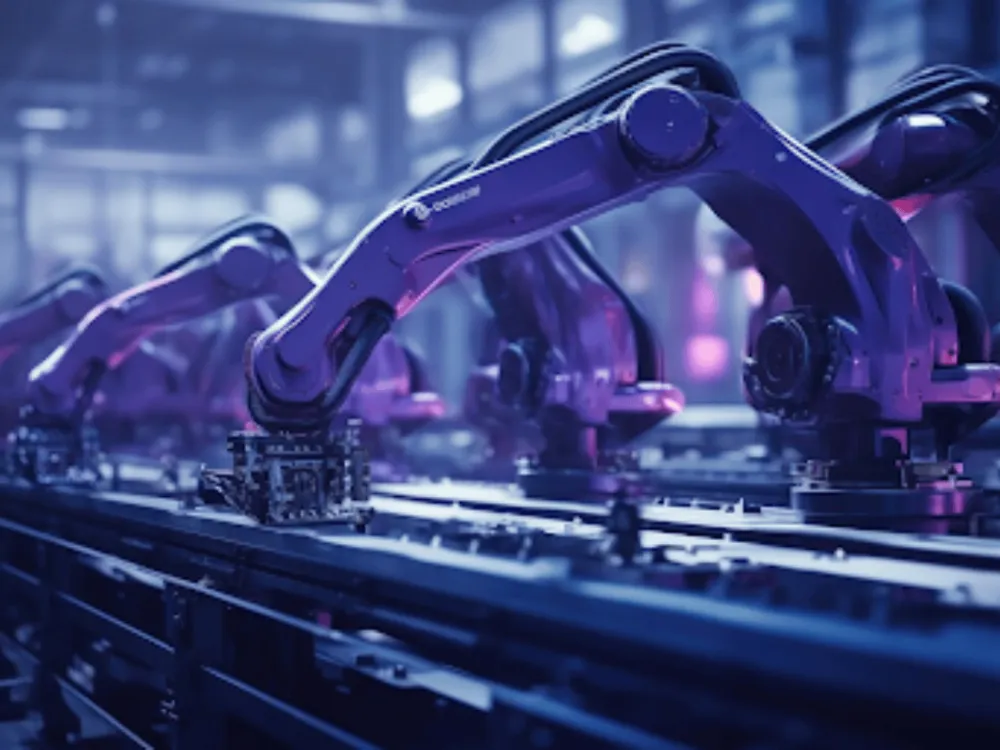
A robotic assembly line.
Making Industry Smart: IoT Transformations in Manufacturing
Why are experts referring to the adoption of smart manufacturing methods as a turning point in industrial history? Much of it has to do with the digital transformation and IoT technology.
But what is smart manufacturing, and how can you and your company take advantage of IoT technology?
What is Smart Manufacturing?
The industry has yet to decide on a definitive definition of smart manufacturing. However, it's generally agreed upon that smart manufacturing includes using computer technology to improve the manufacturing process.
Typically, this involves some level of artificial intelligence enabling machines to capture data, alter procedures, and adjust techniques without requiring direct human intervention. In other words, it's machines passing information back and forth between each other. The machines operate as a cohesive unit bent on improving.
Just as the smart items in your home communicate with each other, so do the machines on the production floor. It's the internet of things in manufacturing.
Making Industry Smart: IoT Transformations in Manufacturing
There are countless ways IoT lends itself to transforming manufacturing, but let's focus on three:
- Integration
- Customization
- Scalability
Integration
IoT doesn't require massive retooling of a manufacturing facility. Its sensors and other tools are not highly invasive. They incorporate themselves well within the existing environment.
The underlying technology is not entirely foreign. Companies contemplating IoT are likely already modern computer-reliant operations.
So, the transition to IoT doesn't require a massive leap in understanding. It's simply the application of principles and subsidiary technology familiar to tech users.
Customization
Your facility may be unlike all others. Your uniqueness, however, doesn't preclude the use of smart technology. IoT applications in manufacturing are limited only by your imagination. IoT software development technicians can devise ways to use the technology to improve your production regardless of your product.
Scalability
IoT in manufacturing industry is scalable to meet your demands. For example, you may have manufacturing equipment in one location or dozens. In either case, IoT can monitor and analyze your production runs. It can also schedule and synchronize machines at different locations.
The Benefits of IoT in Manufacturing
What benefits would IoT bring to your business? Notice some of the advantages it has given other enterprises.
Improves Worker Safety
Companies can use manufacturing IoT devices to continually monitor the health of employees likely to encounter dangerous conditions in the work environment. For example, sensors can capture real-time data regarding biohazards, such as contaminated air, noise levels, and rising or falling temperatures.
The sensors are more reliable than previous tools because of their specificity and quick response. Traditional warning systems may have needed a much higher level of toxicity before issuing an alert. Often this was because they took a reading of a massive area like a factory's production floor.
However, IoT allows for more targeted information. Individual employees could receive an alert of danger relevant to them. That means that a worker can take evasive action faster than previously. It also could mean that fewer colleagues become exposed to the toxin.
Eventually, the IoT system can collect enough data to expose reoccurring conditions where hazards threaten worker safety. This information can help employers adjust or redesign work areas to reduce dangerous situations.
Helps With Sustainability
Globally, companies are looking for ways to meet their sustainability goals without disrupting production. IoT offers ongoing feedback, giving supervisors insight into where their facility could improve its energy conservation.
Sensors can monitor the flow of energy and identify flaws in the systems. A processing plant could experience numerous power surges and drops throughout the day. There may be old, inefficient wiring responsible for power leakage. Or outdated equipment could be energy wasters.
Up-to-date information helps decision makers to decide what changes to implement to make the facility more energy efficient. The adjustments could not only result in meeting sustainability goals but also in reducing utility costs.
Tracks Supply Chain Movement
The supply chain has often been shrouded in mystery. It has been a challenge to successfully track the movement of goods and supplies from the beginning of their journey until the end.
There was often little to no explanation for the disappearance of items in transit. Similarly, there might be no conclusive evidence explaining the poor or compromised condition of the material that did make it to its destination.
IoT can shed light on the previously dark corners of the supply chain. Sensors can track the movement of materials each step, from raw materials to end products.
IoT technology can relay important information about storage and transportation conditions. Manufacturers can verify that the optimal humidity and temperature are present, keeping the product safe.
IoT increases a company's predictability. A business will have a much better idea of how to meet the market demands if it knows when supplies will be available for production. Being aware of the location of materials at all times also betters a company's ability to schedule deliveries accurately.
Delivers Insights on Workflow Issues
Manufacturers have long depended on workers to offer suggestions on how to improve workflow. However, that method relied on the subjectivity of the workers.
Would they willingly highlight areas where their department was deficient? Would they admit that they were not following company protocol?
IoT technology removes subjectivity and offers objective observations of a facility's workflow. The system can readily identify the bottlenecks responsible for slowing production.
Smart technology can also tighten quality control. Often, issues exist because there's no consensus on the origin of the problem. One department may blame the other.
Sensors can give unbiased feedback by examining each step of the manufacturing process and pinpointing the moment flaws appear in the product. Such accuracy can help a manufacturer recognize a defect in a crucial part of the production equipment. Or, it could lead to adjusting the way certain materials are handled or processed.
Improving nagging quality control issues can have many positive effects on a workplace. It can reduce costs as less raw material is used to produce the needed quota of finished product. Then, production costs may drop since fewer run sessions are required.
Improved quality control can also bolster the reputation of the product and the manufacturer while raising worker morale.
Preparing Today for the Future of IoT in Manufacturing Industry
The evidence shows that businesses embracing IoT technology put themselves in a better position to withstand the challenges of their industries. They can also more quickly respond to the demands of the market.
In business, adaptability means the difference between success and failure. The need for this quality is only likely to increase. Conveniently, manufacturing IoT solutions help companies to evolve, allowing them to join the future of manufacturing today.